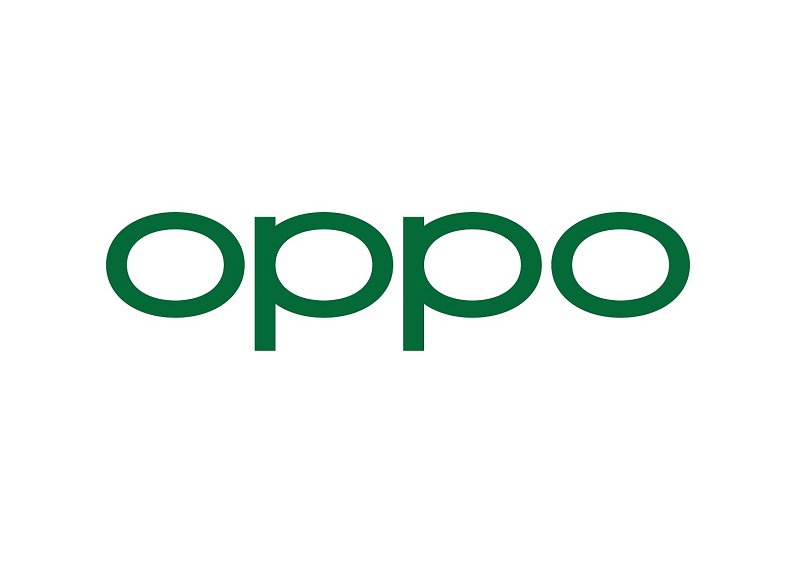
SHENZHEN, CHINA – Media OutReach – 10 March 2022 – The new OPPO Find X5 Pro — a premium flagship handset born from never-before-seen pioneering engineering methods. Available in stunning ceramic and vegan leather, the curved nature of Find X5 Pro’s rear wraps elegantly and organically around the camera housing in an innovative volcano-like design to create an utterly seamless experience, look, and feel, that no other device comes close to matching. Building on the knowledge of creating a similar curved glass rear for Find X3, engineers had to overcome even more substantial challenges to help create a zero-compromise result that met the exact specifications (while surpassing and creating many industry standards in the process)
Find X5 Pro’s ceramic back is made from a microcrystalline material that’s calcined at a temperature of 1000-degrees Celsius to create a texture that reduces fingerprints while being twice as strong as glass, with double the heat dissipation. The downside, however, is that due to its strength, it’s a very tricky and unforgiving material to work with. The thought of creating Find X5 Pro’s precise, organic curved back from such a material seems impossible, but OPPO’s engineers have invented a process which sees the ceramic rear panel carved like a work of art with over 2,000 individual control points used to create its seamlessly organic curves.
Taming the ceramic panel posed some crucial hurdles for engineers to solve, and it took six months of research and development in molding, machining and polishing process to create Find X5 Pro’s iconic curved rear.
A material that’s both incredibly strong and resistant to scratches and drops, ceramic is superior to glass in multiple ways, and was therefore the natural choice for a premium handset like Find X5 Pro, further pushing the boundaries of Find X3’s glass design. The downside to ceramic’s robust properties, however, is that it’s difficult to machine, which is clearly problematic when it comes to producing Find X5 Pro’s unique curved rear design.
Using known existing manufacturing methods resulted in too large a cap between the ceramic rear cover and the camera housing, with less of a smooth curve gradient to boot — an unacceptable outcome. To combat this problem, engineers created a more precise machining method using two blades arranged at a precise 90-degree angle. While this improved the accuracy of the final product, however, the appearance of a straight-edged cutting line surrounding the sides of the ceramic cover, along with visible cutting marks from the machine blade lines.
The solution was the creation of a completely new lift edge polishing process which refined the machined edges for a smoother, properly finished look. Initially, however, it was apparent that removing the manufacturing marks also ended up taking away too much of the ceramic material itself away, making the rear panel too small to properly fit the handset. To overcome this, engineers had to meticulously polish the ceramic’s edges in multiple stages, using a four-axis polishing machine and micron-level diamond powder. Results from polishing stages were checked at regular intervals to then make minute, precise adjustments down to a staggering 0.005mm. A perfectly machined, premium ceramic rear cover that takes five whole days to produce, with a yield of 97% compared to 87%.
One of the major design pain points in smartphones are their camera housing solutions. Most phones have unsightly raised bumps that dominate the design without adding excitement or finesse. Beyond the shape, OPPO’s engineers had to decide how to blend the lenses into the housing itself without any ugly protrusions or camera rings.
Removing the camera lens ring for a cleaner look means that the lens itself must be precisely positioned so that it’s neither too high nor too low. Too high and the lens will be vulnerable to damage. Too low, it will lose the premium feeling of flushnessflow, while being able to feel a dip in the surface.
The upshot of this is that the perfect placement of the camera lenses under the ceramic housing was determined to be 0.10mm, or the thickness of a human hair. As a result of direct assembly, however, this number would often reach the thickness of two hairs. This seems utterly insignificant on paper, but anything less than perfect was simply not good enough.
To combat this, ceramic battery covers were split into three groups based on their incredibly small variations of thickness. The three lenses for Find X5 Pro were also grouped based on their thickness, and then matched to their closest ceramic cover to reach the perfect, precise depth in the camera housing.
OPPO has invested millions to develop specialised automated equipment to group matching lenses and rear covers automatically.
In a world where smartphones are churned out to offer a minimal viable experience, however, OPPO’s commitment to precision and perfection stands out. Devices like Find X5 Pro are the embodiment of hard work, dedication, and countless hours spent in the pursuit of the absolute very best product possible.
With new strides and discoveries being made continuously, OPPO will continue to lead the way for smartphone innovation, with new generations being built on the years of experience and learning before them.
#OPPO